Alcast Company - Truths
The Ultimate Guide To Alcast Company
Table of ContentsThe Alcast Company PDFsSome Ideas on Alcast Company You Should KnowFascination About Alcast CompanySome Ideas on Alcast Company You Should KnowThe Of Alcast CompanyRumored Buzz on Alcast Company
Chemical Comparison of Cast Aluminum Alloys Silicon promotes castability by decreasing the alloy's melting temperature level and boosting fluidity throughout casting. Furthermore, silicon adds to the alloy's toughness and wear resistance, making it beneficial in applications where sturdiness is crucial, such as automobile parts and engine elements.It additionally enhances the machinability of the alloy, making it much easier to refine right into completed items. In this way, iron adds to the general workability of aluminum alloys. Copper enhances electric conductivity, making it helpful in electric applications. It likewise improves deterioration resistance and includes in the alloy's general stamina.
Manganese adds to the toughness of light weight aluminum alloys and improves workability (Aluminum Castings). It is typically used in wrought aluminum items like sheets, extrusions, and profiles. The presence of manganese aids in the alloy's formability and resistance to breaking during fabrication procedures. Magnesium is a light-weight aspect that provides strength and effect resistance to aluminum alloys.
The Main Principles Of Alcast Company
Zinc boosts the castability of aluminum alloys and helps regulate the solidification process during casting. It enhances the alloy's stamina and hardness.
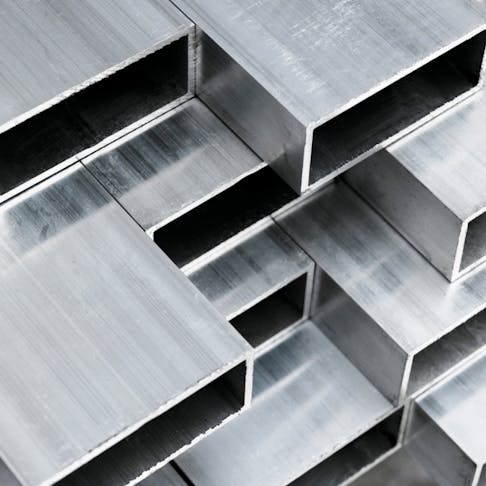
The primary thermal conductivity, tensile strength, return strength, and prolongation differ. Amongst the above alloys, A356 has the highest thermal conductivity, and A380 and ADC12 have the lowest.
Get This Report about Alcast Company
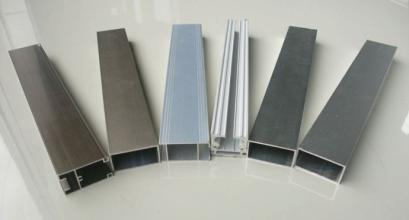
In accuracy casting, 6063 is fit for applications where intricate geometries and premium surface area finishes are extremely important. Instances include telecommunication units, where the alloy's superior formability enables streamlined and aesthetically pleasing layouts while keeping structural stability. In the Illumination Solutions industry, precision-cast 6063 components produce sophisticated and effective lights fixtures that need complex shapes and excellent thermal performance.
The A360 displays superior prolongation, making it excellent for facility and thin-walled parts. In accuracy spreading applications, A360 is fit for markets such as Customer Electronic Devices, Telecommunication, and Power Devices.
Alcast Company Things To Know Before You Get This
Its distinct buildings make A360 an important selection for accuracy casting in these markets, improving product toughness and quality. aluminum foundry. Aluminum alloy 380, or A380, is an extensively used casting alloy with a number of distinct attributes.
In accuracy casting, light weight aluminum 413 beams in the Customer Electronic Devices and Power Devices industries. This alloy's exceptional rust resistance makes it an exceptional option for outdoor applications, guaranteeing resilient, long lasting items in browse this site the discussed sectors.
The Single Strategy To Use For Alcast Company
Once you have actually chosen that the light weight aluminum die casting process is suitable for your job, a crucial next action is deciding on the most proper alloy. The light weight aluminum alloy you select will significantly influence both the spreading procedure and the buildings of the final product. Since of this, you should make your choice thoroughly and take an informed method.
Establishing the most suitable light weight aluminum alloy for your application will imply evaluating a large range of characteristics. The initial category addresses alloy attributes that affect the production procedure.
How Alcast Company can Save You Time, Stress, and Money.
The alloy you choose for die casting straight influences several elements of the casting procedure, like just how simple the alloy is to collaborate with and if it is prone to casting issues. Warm fracturing, also referred to as solidification cracking, is a common die casting issue for aluminum alloys that can result in interior or surface-level rips or fractures.
Particular light weight aluminum alloys are much more vulnerable to hot cracking than others, and your option ought to consider this. It can harm both the cast and the die, so you ought to look for alloys with high anti-soldering properties.
Deterioration resistance, which is already a significant quality of aluminum, can differ significantly from alloy to alloy and is a crucial characteristic to take into consideration depending upon the ecological problems your item will be revealed to (Foundry). Wear resistance is another residential property generally looked for in light weight aluminum items and can distinguish some alloys